خط کوتینگ
خط کوتینگ (پوشش دهی)، سیستمی است که امکان پوشش سطحی هر نوع پودر معدنی را با متنوعترین مواد افزودنی اعم از پلیمر، اسید استئاریک و ... فراهم میکند.
این سیستم از یک آسیاب پین میل دو جهته استفاده میکند که میتواند تنشهای برشی بالایی را القا کرده و کارآمدترین اثر ضد آگلومره را ایجاد کند.
آسیاب پین میل دوجهته: پین میل ارتقا یافته جهت تولید مواد ریز و کوتینگ مواد
خردایش
با روتورهای پین دیسک دو جهته، سرعت لبه روتور در این آسیاب به بیش از 200 متر بر ثانیه میرسد که امکان خردایش مواد معدنی نرم تا نیمه سخت را با اندازه ذرات مطلوب، فراهم میکند. کنترل مستقل سرعت و جهت چرخش پین دیسک، درجه بالایی از انعطافپذیری را میدهد. جریان هوای عبوری از طریق آسیاب به خردایش کمک کرده، دمای محصول را کنترل میکند و محیطی برای انتقال پنوماتیک محصول فراهم مینماید.
در حالت استاندارد، آسیاب یک بدنه فولادی جوش داده شده قوی دارد. در صورت لزوم، آسیاب پین میل دوجهته پکصا را میتوان با فولاد ضد زنگ نیز تولید کرد. تعمیر و نگهداری این آسیاب بسیار آسان بوده و تعویض پین به راحتی انجام میشود.
کوتینگ (پوشش دهی)
خط کوتینگ پکصا، با هدف دستیابی به محصول پوشش دار شده (کوتِد) بسیار همگن با کم ترین میزان مواد افزودنی و با خروجی نهایی عاری از آگلومره، طراحی شده است.
این شرکت یک سیستم مبتنی بر وزن، برای ماده پوشش دهنده طراحی کرده است که در آن جریان جرم به طور پیوسته توسط PLC مانتیتور و کنترل میشود.
ماده پوشش دهنده از طریق یک نازل اتمیزهکننده با سرعت بالا به آسیاب پین میل تزریق میشود، جایی که هوای تحت فشار، جریانی از میلیونها قطره کوچک ماده ذوب شده را ایجاد میکند. تزریق مایع به منطقه ای با نیروهای برشی بالا، اندازه قطرات را حتی بیشتر کاهش میدهد، به این معنی که ذرات کوچک بواسطه قطرات بزرگ به ذرات دیگر "چسبیده" نمیشوند.
کل عملیات کوتینگ مورد نظر در داخل آسیاب پین میل انجام میشود. این فناوری تضمین میکند که پوشش دهی بیش از حد یا اتلاف ماده پوشش دهنده، یا عدم پوشش دهی کافی و از دست رفتن کیفیت محصول وجود نخواهد داشت؛ که این امر میتواند به راحتی با تست واترگلاس یا HCl آزمایش شود.
خط کوتینگ پکصا توان رقابت با نمونههای مشابه اروپایی را داشته و از این روشها جهت تولید پودر با کیفیت استفاده کرده است.
این سیستم از یک آسیاب پین میل دو جهته استفاده میکند که میتواند تنشهای برشی بالایی را القا کرده و کارآمدترین اثر ضد آگلومره را ایجاد کند.

آسیاب پین میل دوجهته: پین میل ارتقا یافته جهت تولید مواد ریز و کوتینگ مواد
فرآیند خردایش و کوتینگ (پوشش دهی)
خردایش
با روتورهای پین دیسک دو جهته، سرعت لبه روتور در این آسیاب به بیش از 200 متر بر ثانیه میرسد که امکان خردایش مواد معدنی نرم تا نیمه سخت را با اندازه ذرات مطلوب، فراهم میکند. کنترل مستقل سرعت و جهت چرخش پین دیسک، درجه بالایی از انعطافپذیری را میدهد. جریان هوای عبوری از طریق آسیاب به خردایش کمک کرده، دمای محصول را کنترل میکند و محیطی برای انتقال پنوماتیک محصول فراهم مینماید.
در حالت استاندارد، آسیاب یک بدنه فولادی جوش داده شده قوی دارد. در صورت لزوم، آسیاب پین میل دوجهته پکصا را میتوان با فولاد ضد زنگ نیز تولید کرد. تعمیر و نگهداری این آسیاب بسیار آسان بوده و تعویض پین به راحتی انجام میشود.
ویژگی های منحصر به فرد خردایش
- آسیاب کردن مواد معدنی نرم و تا نیمه سخت
- طراحی بسیار قابل اعتماد و قوی
- چرخش پین دیسک هابه صورت هم جهت یا دوجهت، بسته به نیاز مواد و کاربرد
- تعمیر و نگهداری آسان و سریع و در نتیجه هزینه های نگهداری کم
کوتینگ (پوشش دهی)
خط کوتینگ پکصا، با هدف دستیابی به محصول پوشش دار شده (کوتِد) بسیار همگن با کم ترین میزان مواد افزودنی و با خروجی نهایی عاری از آگلومره، طراحی شده است.
این شرکت یک سیستم مبتنی بر وزن، برای ماده پوشش دهنده طراحی کرده است که در آن جریان جرم به طور پیوسته توسط PLC مانتیتور و کنترل میشود.
ماده پوشش دهنده از طریق یک نازل اتمیزهکننده با سرعت بالا به آسیاب پین میل تزریق میشود، جایی که هوای تحت فشار، جریانی از میلیونها قطره کوچک ماده ذوب شده را ایجاد میکند. تزریق مایع به منطقه ای با نیروهای برشی بالا، اندازه قطرات را حتی بیشتر کاهش میدهد، به این معنی که ذرات کوچک بواسطه قطرات بزرگ به ذرات دیگر "چسبیده" نمیشوند.
کل عملیات کوتینگ مورد نظر در داخل آسیاب پین میل انجام میشود. این فناوری تضمین میکند که پوشش دهی بیش از حد یا اتلاف ماده پوشش دهنده، یا عدم پوشش دهی کافی و از دست رفتن کیفیت محصول وجود نخواهد داشت؛ که این امر میتواند به راحتی با تست واترگلاس یا HCl آزمایش شود.
خط کوتینگ پکصا توان رقابت با نمونههای مشابه اروپایی را داشته و از این روشها جهت تولید پودر با کیفیت استفاده کرده است.
ویژگی های منحصر به فرد کوتینگ
- به حداقل رساندن ماده پوشش دهنده
- دستیابی به یک لایه کامل از ماده پوشش دهنده
- جلوگیری از تشکیل آگلومره پس از فرآیند پوشش دهی (کوتینگ)
- مصرف کم انرژی
- عمر طولانی کیسه های فیلتر
- طراحی فشرده
خط کوتینگ کربنات کلسیم
رایجترین کاربرد خط کوتینگ، پوشش کربنات کلسیم (CaCO3( با استئاریک اسید است. کربنات کلسیم آسیاب شده در محدوده 3 تا 45 میکرون، به عنوان ماده اولیه انتخاب میشود که پوشش دهی آن میتواند منجر به ارزش افزوده قابل توجهی گردد. صنعت پلاستیک به کربنات کلسیم کوت شده (پوشش داده شده) نیاز وافری دارد.
این محصول با پاشش مایع (غیرمحلول) همگن شده به ماده اولیه بدست میآید. یکی از ویژگی های خط کوتینگ این شرکت این است که عبور دوباره محصول کوتِد از کلاسیفایر (سپراتور) ضروری نیست. چرا که با کنترل فرآیند تولید مواد روکش شده در پایین دست آسیاب پین میل، از تشکیل آگلومره جلوگیری میشود و اسید استئاریک در سریعترین زمان ممکن جامد میشود.
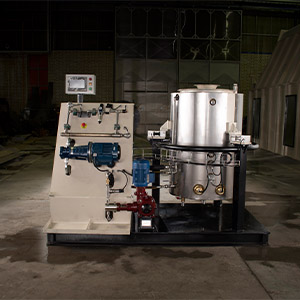
تصویر زیر، شماتیک سیستم ذوب و سپس اتمیزه کردن استئاریک اسید در ترکیب با آسیاب پین میل دو جهته برای کوتینگ کربنات کلسیم را نشان میدهد.
تغذیه مواد پوشش دهنده
استئاریک اسید (A) از هاپر به وسیله اسکرو فیدر (1) به بوته ذوبکننده (2) وارد می شود. میزان تغذیه استئاریک اسید در ورودی بوته ذوب و همچنین میزان خروجی محصول از بوته، توسط مکانیزم لودسل اندازهگیری میشود.
بوته ذوبکننده به طور غیرمستقیم گرم میشود. یک عنصر حرارتی، سطح حرارت را بالاتر از نقطه ذوب نگه میدارد و یک میکسر اضافی تضمین میکند که گرما در سراسر بوته یکنواخت باقی میماند. از آنجایی که دما در سطح ثابتی نگه داشته میشود، انرژی گرمایشی ذخیره میشود.
درجه کوتینگ (پوشش)
استئاریک اسید مایع از طریق لوله های ویژهای به بیرون از بوته ذوب منتقل میشود. یک پمپ وظیفه پمپاژ مقدار تعیین شده استئاریک اسید را بر عهده دارد. درجه کوتینگ تابعی از تنظیم مناطق گرمایشی است. این روش کنترلی منجر به کاهش اتلاف استئاریک اسید و پوشش یکنواخت محصول میشود.
فرآیند اتمیزه کردن
یک نازل دو جزئی، استئاریک اسید را با هوای فشرده شده اتمیزه میکند. نازل دو جزئی با استفاده از شیر برقی کنترل میشود. مقدار تزریق استئاریک اسید به خط تولید پایین دستی کنترل میشود.
اندازه گیری تغذیه
کربنات کلسیم (B) با استفاده از یک اسکرو فیدر (1) قابل تنظیم به طور یکنواخت تغذیه میشود. یک تله مغناطیسی با تضمین حذف هر گونه ماده فلزی، جریان یکنواختی از محصول را تامین میکند. فلومتر برای نظارت بر عملکرد استفاده میشود.
پردازش
برای اطمینان از اختلاط موثر استئاریک اسید با کربنات کلسیم، از آسیاب پین میل دو طرفه (3) استفاده میشود. استئاریک اسید با روشی مناسب به هسته آسیاب منتقل میشود تا پوشش دهی کربنات کلسیم در میان پین دیسکها و چرخش موثر آنها رخ دهد. بدین ترتیب هیچ مقداری از کربنات کلسیم راه گریز از پوشش دار شدن ندارد! سرعت محیطی بالای پین دیسکها و گرمایش همزمان، تماس تمام سطح را تضمین میکند و محصولی با کیفیت فوق العاده تولید میکند.
چرخه هوا
یک واحد گرمایشی، دمای هوای در گردش را در یک سطح ثابت نگه میدارد. کنترل دما در نقطه ذوب برای جلوگیری از ایجاد لکههای سیاه (به دلیل گرمایش بیش از حد) یا آگلومره (به دلیل افت سریع دما) در محصول، مهم است.
فیلتراسیون
به دلیل خواص فیزیکی تغییر یافته، جدا کردن محصولات کوتِد (C) از جریان هوا بسیار دشوار است، اما بگ فیلترهای پکصا (5) دقیقاً مطابق با این الزامات طراحی شده است.
کاربری
مواد اولیه: کربنات کلسیم (GCC و PCC)، کائولن، تالک، میکا، گرافیت، سولفات باریم، کربن بلک، کربن بلک سفید، هیدرات منیزیم، اکسید روی، اکسید آلومینیوم.
مواد پوشش دهنده: استئاریک اسید، عامل جفت کننده آلومینات، عامل جفت کننده تیتانات، عامل جفت کننده سیلان.
خط کوتینگ کربنات کلسیم
رایجترین کاربرد خط کوتینگ، پوشش کربنات کلسیم (CaCO3( با استئاریک اسید است. کربنات کلسیم آسیاب شده در محدوده 3 تا 45 میکرون، به عنوان ماده اولیه انتخاب میشود که پوشش دهی آن میتواند منجر به ارزش افزوده قابل توجهی گردد. صنعت پلاستیک به کربنات کلسیم کوت شده (پوشش داده شده) نیاز وافری دارد.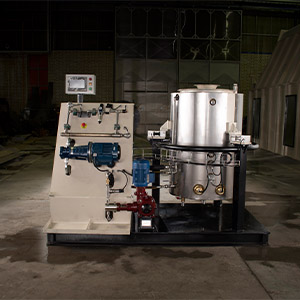
تصویر زیر، شماتیک سیستم ذوب و سپس اتمیزه کردن استئاریک اسید در ترکیب با آسیاب پین میل دو جهته برای کوتینگ کربنات کلسیم را نشان میدهد.
تغذیه مواد پوشش دهنده
بوته ذوبکننده به طور غیرمستقیم گرم میشود. یک عنصر حرارتی، سطح حرارت را بالاتر از نقطه ذوب نگه میدارد و یک میکسر اضافی تضمین میکند که گرما در سراسر بوته یکنواخت باقی میماند. از آنجایی که دما در سطح ثابتی نگه داشته میشود، انرژی گرمایشی ذخیره میشود.
درجه کوتینگ (پوشش)
فرآیند اتمیزه کردن
اندازه گیری تغذیه
پردازش
چرخه هوا
فیلتراسیون
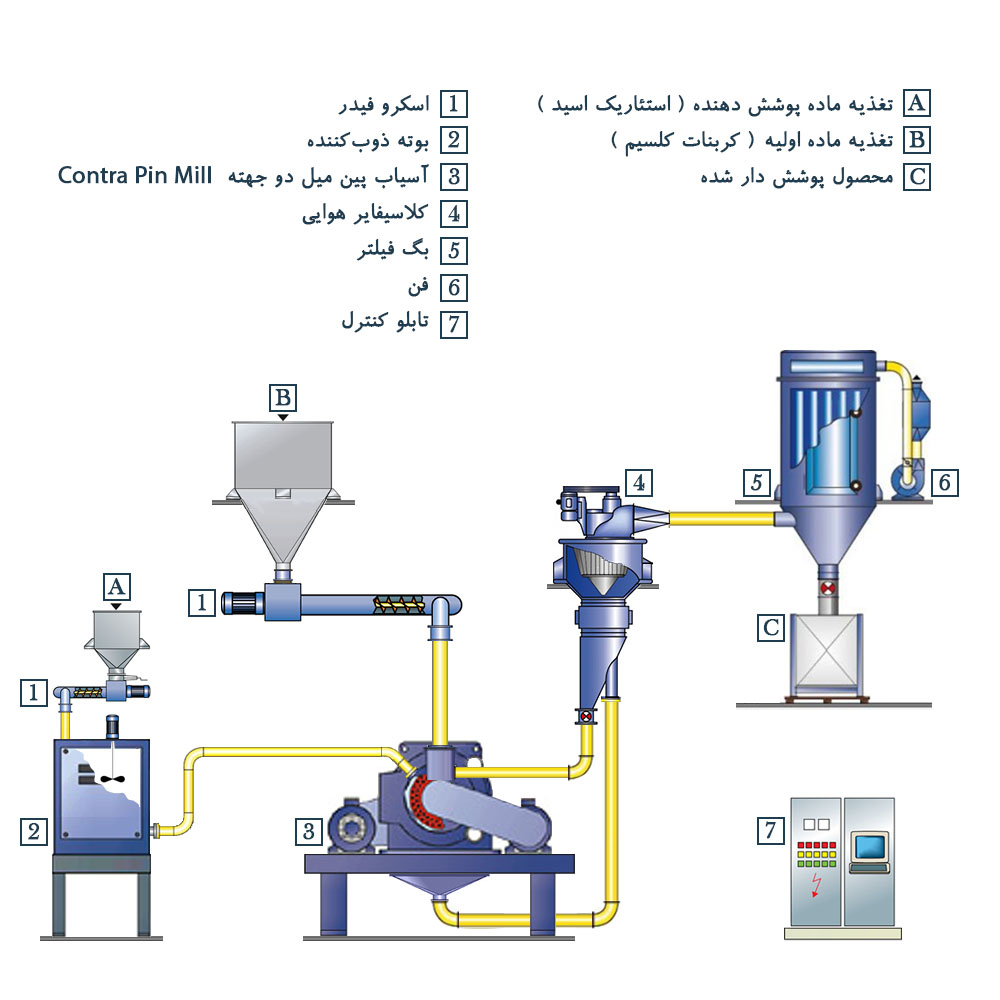
کاربری
مواد اولیه: کربنات کلسیم (GCC و PCC)، کائولن، تالک، میکا، گرافیت، سولفات باریم، کربن بلک، کربن بلک سفید، هیدرات منیزیم، اکسید روی، اکسید آلومینیوم.
مواد پوشش دهنده: استئاریک اسید، عامل جفت کننده آلومینات، عامل جفت کننده تیتانات، عامل جفت کننده سیلان.